How to make production cost efficiencies can be achieved by reducing or finding expenses related to the production process, for example, by reducing the costs of raw materials, labour, and overhead. The goal is that the company can get optimal profits. Let’s see the full explanation in this article.
The Causes of High Production Costs
In the production process, of course, some costs must be incurred by the company so that the production process runs smoothly.
Unfortunately, in the production process, there can also be waste in the use of raw materials and wastage of employee working time so that productivity does not match what the company expects; it can even be in the form of wasted working capital to buy various production equipment and machinery.
5 Ways to Make Production Cost Efficiency
1. Evaluation of Waste of Raw Materials
The most common problem related to raw materials is the effort to buy raw materials at the lowest prices to provide greater profits for the company.
However, poor-quality raw materials have a greater risk of failure, and the quality of production results is also not good. Instead of making a profit, this can cause the company to experience more losses.
For this reason, re-evaluate the use of raw materials as a whole. Make sure production employees can maximize the use of raw materials and do not waste raw materials (raw materials are destroyed, damaged due to negligence, expired due to lack of inspection and supervision, and so on.
The next important thing, avoid having large amounts of raw material inventory. This is because business capital is being held back due to piles of raw materials that cannot be sold immediately. In addition, it minimizes the possibility of expired or damaged raw materials due to storage.
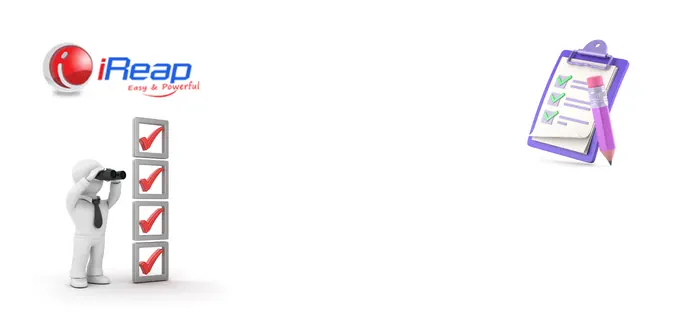
2. Planning in Purchasing Raw Materials
Make a plan to purchase raw materials carefully and thoroughly. Establish cooperation with suppliers who can provide good quality raw materials at competitive prices. In addition, buy raw materials as needed plus a little as a reserve.
Make detailed records and periodically calculate how much raw material is used in one production. Neat and well-organized records will make it easier for you to procure better raw materials for your next purchase.
3. Efficient Labor and Prevent Waste of Working Time
Cost efficiency for labour does not mean you need to do labour counts. Instead, you need to make sure all the workforce you have can work productively well and not be lazy (wasting work time).
There are several ways you can do to streamline labour costs, including:
- Create a work schedule so that employee performance is maintained and does not tire employees.
- Adjusts wages for employees in the production department based on working time and work results. The goal is that they don’t waste working time or eat blind wages.
- Ensure employee welfare to reduce turnover. This can save the company’s expenses, considering that the recruitment costs are much higher to get workers whose performance is still uncertain.
- Ensuring work safety and a conducive working atmosphere. This method will increase workers’ comfort in the production process and make them more loyal to the company.
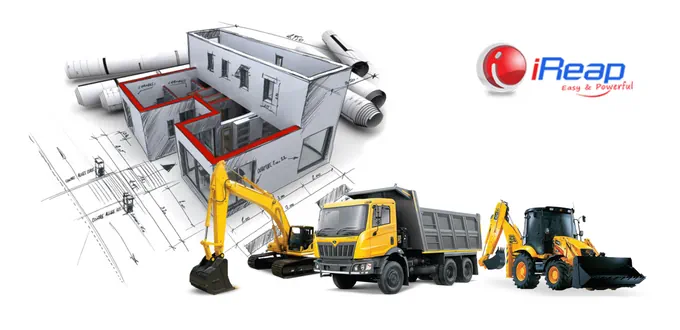
4. Maximizing Production Machinery and Equipment Performance
Many companies experience large expenses for the maintenance and repair of production machines and equipment.
The machine is often damaged and cannot be used, even though the duration and usage time are still small.
The reason is improper use of the machine; the machine does not get “rest time” and rarely gets maintenance. It could also be because workers must learn how to operate the device properly.
To prevent this, you have to ensure the employees in charge of operating the production machines and equipment understand how the machines work.
In addition, carry out periodic maintenance of machines and equipment and make it a habit to check the device’s condition before starting production.
5. Reduce Overhead Expenses and Waste of Working Capital
Reduce overhead costs associated with the production process. For example, reducing overtime pay (and making work hours more efficient) reduces electricity costs by turning off electricity when working hours end. Save water use by not wasting water or allowing water to flow continuously and be wasted.
To minimize all costs related to the production process, you must have a record of all these costs first. Detailed descriptions, including inventory records, make it easier for you to analyse and evaluate production costs. You can use a free cashier application or a paid cashier application to facilitate the recording of all prices and inventory. Remember also to find out what production cost is and the Components of Production Cost.